VOL. 08 | ISSUE 1 | Spring 2025
Olmsted
Optimistic
About 2025
Lauds Gains in Safety,
Discusses Priorities for 2025
Improvement in safety performance driven by a continued focus in that area and a continued focus on the fundamentals highlights 2024’s performance and the possibilities for an “even better” 2025.
In a wide-ranging interview that addressed 2024’s successes and 2025’s opportunities, Josh Olmsted, President and Chief Operating Officer-Americas, discussed the improved safety results, the importance of connecting with site team members and the new Reinvent Mining strategic pillar.
Introduced as one of this year’s strategic themes, Reinvent Mining joins Execute for Value, Leach to the Last Drop, Maintenance and Reliability, and Employee Experience as the areas where employees should be spending their time in 2025.
With the new year in full swing, Olmsted reflected on a host of topics to help set the agenda for the year ahead.
As you look back at 2024, how would you evaluate the performance of North America operations?
I’ll start with safety. While we didn’t end up where we wanted to be, we saw improvements across the board in the safety space. We had the best TRIR (total recordable incident rate) since 2015, and we beat our goal for the year, so that’s an achievement worth pointing out. Also, we had a target to reduce our overall high-energy events by 25 percent. We didn’t achieve that, but we did see a reduction. We went from 50 high-energy events in 2023 to 43 in 2024. In reviewing the year, the safety improvement that we saw was most significant.
From a production perspective, we didn’t achieve our targets, but we continue to see improvements across the board. More and more of our operations are running at a stable and reliable state than they were at the beginning of 2024. Similar to production, we saw some improvements in our unit costs and cost management over the year. While we didn’t achieve all our targets, I would say by the way we finished the year on a good trajectory that it was a solid performance.
To what do you attribute the organization’s improved safety performance?
I think it’s really focusing on getting back to the basics. That’s not only applicable to safety; it’s applicable to everything in our business. It’s about getting out in the field and having the right conversations at every level of the organization and ensuring there is clarity and alignment about what is the most important work we’re doing day in and day out. There also has been a continued focus on how we are having those conversations. The global safety stand down really helped galvanize everyone to understand that we all have a responsibility to go home safely every day.
It was about making sure our actions backed up our words, and each of us is accountable to that. That’s just one of many examples of why I think we continued to build on the momentum.
Getting back to the basics and focusing on the fundamentals have been themes of your conversations with employees. What do those things mean to you?
It’s just understanding what drives the business – what are those basic blocking and tackling things. For example, that might be talking about having a shovel set-up in an efficient and productive manner so trucks can back in without having to jockey for position, and the roads are maintained in the right way so the trucks can get to their optimum speed. It’s thinking about and understanding the key metrics we should be watching every single day that drive the business. Whether that’s safety, production or costs, there are certain metrics that drive the business.
There’s more and more information than there has ever been, and you can get dizzy looking at all that information. You can get distracted focusing on the shiny objects. Back to the basics is understanding those fundamental things we need to focus on to drive the business. It’s not just important to understand and monitor the key metrics, but we also must act when we don’t get the expected results.
You have been a big proponent of leadership getting out from behind their desks to spend time with employees in the field. Why is that important?
Safety performance and operational performance are all about people. Leaders need to be in the field observing, having conversations, engaging. I think there is more and more of that going on. Many sites have created intentional space, like the no-fly zone, which is all about getting in the field and making sure you are having the right conversations. It’s not just going out in the field to be out in the field. It’s about knowing what we’re supposed to be doing out there. I’m not just driving around in
the mine or walking around the plant; I’m intentionally observing and seeing how the process is going, looking for opportunities we may have to improve and what our employees need to be successful in doing their work.
Why is that human connection so important?
You have to know your people. It’s not just having a conversation about how the operation is going. It’s asking how they are doing and how their family is doing. At first blush, someone might think, “What does that have to do with work?” Well, if you don’t understand your people, how are you going to really know if everything is right when they come to work. The more you have those conversations and know your people builds this camaraderie, trust, desire to do the right things. It’s fundamental to build relationships with people throughout the organization.
There is a new addition to the 2025 strategic pillars – Reinvent Mining. How does that pillar fit with the other priorities for the year ahead?
As you go through and reflect on where we are, the business needs going forward and what we need to be working on in the near term, then you can figure out the potential value of that work. If I look at the Execute for Value pillar, that’s kind of the ticket to the game. We must do that well to set ourselves up for the future. That’s really about the safe execution of our plans. The other four pillars are about supporting Execute for Value or setting ourselves up for the future.
I think the things we are going to do with Reinvent Mining will be applicable across the board. If you look at our cost profile and the type of operations we have in North America, we have long-lived assets – some of them in operation for 100 years or more, grades that are declining, haul distances that are increasing, cost pressures. As a result of longer hauls, lower grade, inflationary pressures, etc., our operations in the U.S. are become more expensive, which means that if the copper price were to ever drop to $3.50 per pound, then you’re uneconomic.

So, then we’re looking at how can we set ourselves up for success in the future. It’s thinking about what we do day in and day out, looking for ways to drastically change our cost profile so we can better position ourselves to withstand challenges in the future. It’s exciting to think we can have a positive impact on per-unit costs, which can set ourselves up to turn resources we have in the ground into reserves.
What are you most optimistic about when you think of 2025?
For me, it’s seeing the progress we made in 2024 and having the optimism to think about how we can make it even better in 2025. We saw a bunch of improvements across the board, and what’s exciting to me is to see how much opportunity we have in front of us to get even better. That benefits everybody involved, whether that’s the guy with a shovel cleaning up under the conveyor, the communities where we operate or our investors. When we can get better, it’s just a win-win all the way around.
As employees consider the 2025 pillars and what they can do to support the business, what do you want them to keep top of mind?
It’s important to have clarity on what we are going to do, which the objectives help us with. But I think it’s equally important to decide what we are NOT going to do. That’s harder sometimes. I’ve asked people to step back from the “chaos” of the day to day and ask yourselves what you are going to do and to be purposeful about and what you are NOT going to do. That way, you can free up space to ensure we don’t get distracted from things that are not in support of achieving those objectives. ■

Execute for Value
Keeping Jobsites Safe Through Hazard Recognition
As rain approached the Safford mine, Haul Truck 60 emptied its load at the dump face when a torque converter pump malfunctioned, preventing the bed from lowering. It seemed like a routine repair when the three mechanics – including Diesel Diagnostic Mechanic Daniel Burns – arrived to fix it.
Burns locked out the area and made his initial inspection. As the team worked, a steady rain began.
Rather than focus exclusively on the task at hand, Burns remained aware of his environment and noticed a deep crack forming under the rear axle due to the rain and truck’s weight. Recognizing the safety hazard, he stopped work, cleared the area and notified a supervisor. Two bulldozers later towed the truck to safety.
“I don’t hesitate if something’s not right,” Burns said. “I want to keep everybody safe, including myself. We watch out for each other out here.”
Vicki Seppala, General Manager-Safford, praised the team for “recognizing risk, stopping work, getting the right people involved and taking action to improve safe work conditions before resuming work.”
Awareness Builds Safety Confidence
The incident in January highlights the importance of situational awareness, hazard recognition and the confidence to stop work, said Stacey Koon, Vice President-Safety, Health and Technical Training.
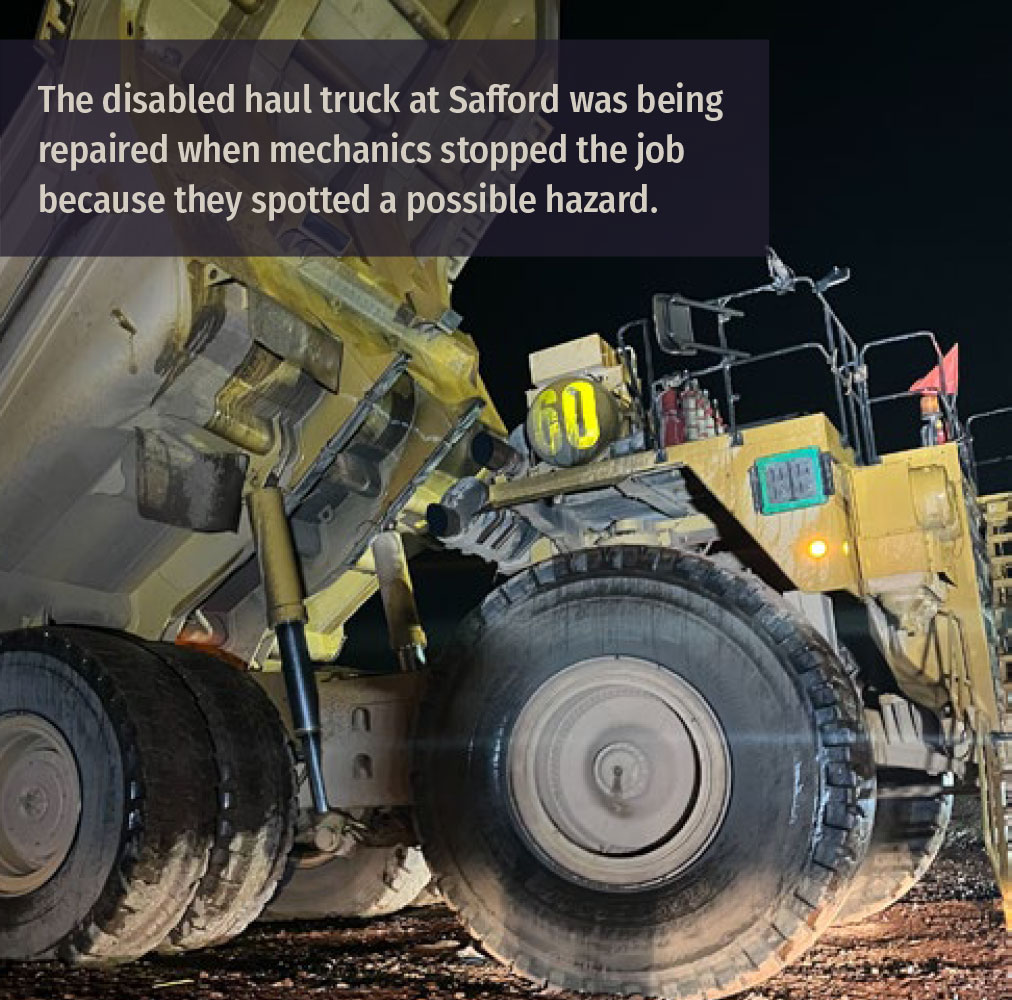
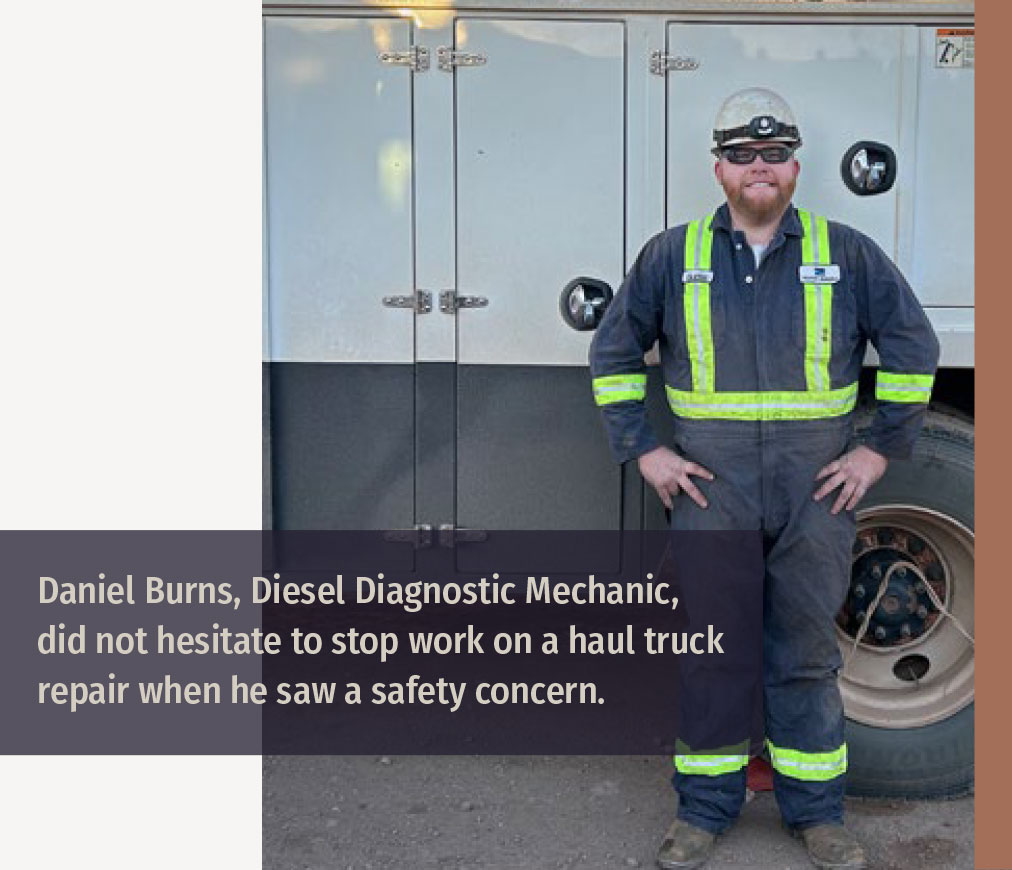
The company’s core values empower employees to stop work if it’s unsafe, highlighting they have both the right and the obligation to do so until it is safe to proceed. Equally important are maintaining a heightened awareness of their surroundings and recognizing potential workplace hazards.
“It’s really hard to stop work if you don’t recognize the hazard first,” Koon said. “People must actively look for risks all the time. If you don’t constantly look for what’s going to hurt you, you can’t possibly stop work. You must take that responsibility. It has to be embedded in your core.” Safety is the core value at Freeport and one of the company’s strategic pillars for success in the Americas.
Freeport has numerous policies and programs to keep its workers safe by helping them identify risks and ensuring they have the right skills, training and tools to work safely. These include fatal risk management, workplace exams, job safety analyses and inspections.
Taking the time to recognize risks and hazards is another important part.
“People must actively look for risks all the time. If you don’t constantly looking for what’s going to hurt you, you can’t possibly stop work. You must take that responsibility. It has to be embedded in your core.”
STACEY KOON | VICE PRESIDENT-SAFETY, HEALTH AND TECHNICAL TRAINING
Watching for Trouble
One simple practice is the 20/20/20 rule: Take 20 seconds every 20 minutes to check 20 feet around you, Koon said. When performing a job, it’s easy to tune out your surroundings.
Following this rule keeps you alert to your changing environment and helps you assess the safety of yourself and others, she said.
The tragic loss of two contractor workers in 2024 was a solemn reminder of the importance of safety in every task, every day. However, the Americas organization did end the
year with significant progress.
The Total Recordable Incident Rate was down 22 percent from the previous year. It is the best performance since 2015.
High-risk incidents, those most likely to cause death or serious injury, also declined by 12 percent. While this missed the goal of a 25 percent reduction, the trend is in the right direction.
Much of the credit goes to site managers and line supervisors for setting high expectations about safety, promoting hazard awareness, and holding themselves and employees accountable, Koon said.
Staying “super focused” on reducing high-risk incidents while continuing to improve TRIR performance remains the priority for 2025.
“To meet our goals, we don’t need to do anything new or ask people to do anything new,” Koon said. “We simply need to use the tools and expertise we already have. Safety is a core value for us, and we’re all capable of Safe Production. It’s a matter of upholding this value by keeping ourselves and others safe.”
Leach to the Last Drop
Transforming with Innovation
If all goes according to plan, this is the year that Freeport’s innovative leaching initiative transforms from maximizing what is known and available to deploying what is still being invented.
So far, Leach to the Last Drop has relied mostly on better use of known technology and techniques guided by data, testing, and trial and error. That has been successful. Last year, the innovative leaching methods produced 214 million pounds of copper that otherwise would not have been produced.
Beginning in 2025, there will be a greater reliance on new products and methods that still are in development or have not been deployed on a large scale, said Justin Cross, Vice President-Operational Improvement.
The Leach to the Last Drop initiative aims to achieve an annual run rate of 300 million to 400 million pounds of new copper by the end of 2025. Of that, about 10 percent will come from new innovations. The rest will be through better use of existing technology and techniques.
In 2026, the amount of copper produced by new products and methods will increase to about 33 percent. And by 2029, innovation will account for more than half of the copper produced, or about 387 million of the nearly 700 million pound annual run rate expected to be reached that year.
Making that transition will require new products and extraction methods that are being developed and deployed this year.
“We have a whole laundry list of tactics in the pipeline that we’re looking to start trying this year,” Cross said. “It’s a huge year. We’ve got to build a bunch of stuff in 2025, and the pounds will largely be produced in 2026.”
Leach to the Last Drop is the company’s initiative to use innovative leaching techniques to unlock an estimated 40 billion pounds of copper in existing stockpiles that once was thought unrecoverable. It is one of the strategic themes that help the company safely achieve its production targets by being the Best at the Basics.
Initial steps included things like covering stockpiles with plastic to increase heat retention and stringing leach lines to side slopes and other areas that historically have not been treated. Those new uses of old technology have paid off. In 2024, the techniques produced 214 million pounds at a cost of less than $1 pound, including capital and research expenses.
“We have a whole laundry list of tactics in the pipeline that we’re looking to start trying this year. It’s a huge year. We’ve got to build a bunch of stuff in 2025, and the pounds will largely be produced in 2026.”
JUSTIN CROSS | VICE PRESIDENT-OPERATIONAL IMPROVEMENT
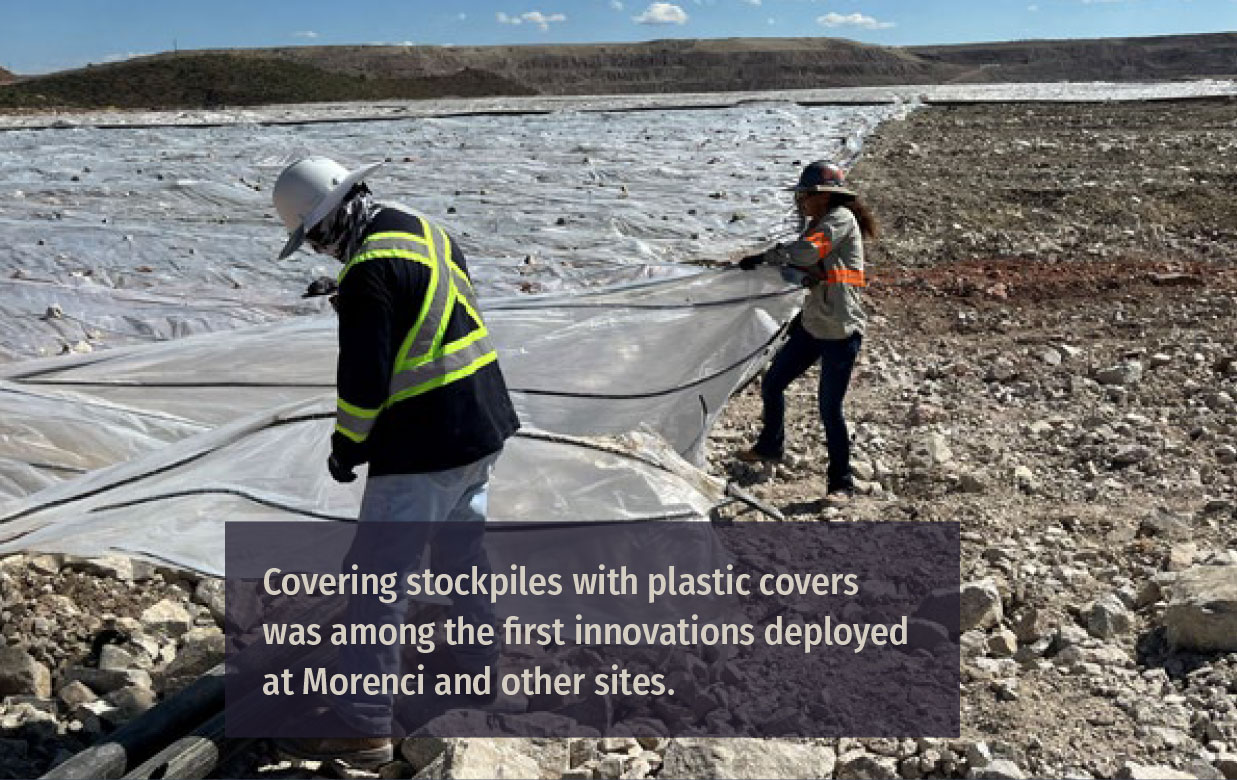
Innovation Critical for Future
- The Leach to the Last Drop initiative aims to achieve an annual run rate of 300 million to 400 million pounds of new copper by the end of 2025.
- About 10 percent will come from new innovations. The rest will be through better use of existing technology and techniques.
- In 2026, the amount of copper produced by new products and methods will increase to
about 33 percent. - By 2029, innovation will account for more than half of the copper produced, or about 387
million of the nearly 700-million-pound annual run rate expected to be reached that year.
This year, there are several major projects in the Americas to make the transition through innovation, including:
- Additive testing and deployment being done at Morenci, Chino and El Abra. The company is involved in research using machine learning and artificial intelligence to develop new leaching additives that will increase copper production, especially in chalcopyrite. Beyond the chemicals themselves, application methods are being developed and tested so when the right products are found, they can be deployed quickly.
- Using heated raffinate to enhance recovery at Morenci and El Abra.
- Building the “Perfect Pile” at Chino. Rather than retrofitting sensors and other technology into existing stockpiles, as has been done so far, this project is to build a new leach pile from scratch and use it as something of a copper-producing laboratory. Sensors will be placed to optimize data collection. Techniques like air injection or changing variables such as temperature or leach solution grades can be tested to maximize copper recovery.
Maintenance and Reliability
Ongoing Strategies Hold Key to Production Improvements
No geological survey conducted. No core sample drilled. No haul truck purchased.
And yet, it’s as if a new mine appeared overnight, instantly boosting production without the site having to invest time and money into more construction or equipment. This isn’t just a hypothetical scenario – it’s the potential being realized by Freeport’s Maintenance and Reliability team through two powerful words: asset efficiency.
Although it has been pursued in different forms through the years, the recognition of how even minor improvements can have major impacts when spread across the entire company had become a guide by which Maintenance and Reliability guided their efforts.
“This strategy of continuous improvement isn’t just about preventing breakdowns. It is about economically managing our assets throughout their entire lifecycle to consistently meet our committed production plans.”
JUN MONTES | GENERAL MANAGER MAINTENANCE-FM AMERICAS
Now, Jun Montes, General Manager Maintenance-FM Americas, is continuing to chart that course, with improved asset efficiency, or the level that equipment is running closer to its full potential, as a core component of Freeport’s objectives.
“The path forward is clear,” Montes said. “This strategy of continuous improvement isn’t just about preventing breakdowns. It is about economically managing our assets throughout their entire lifecycle to consistently meet our committed production plans. As we do this, we will continue to raise the bar in our journey to unlocking the true potential of every asset in the company’s portfolio.”
And already those efforts are setting up Freeport for future success. While not enough to offset shortfalls elsewhere, ensuring equipment ran more consistently contributed an additional 50 million pounds of copper in 2024.
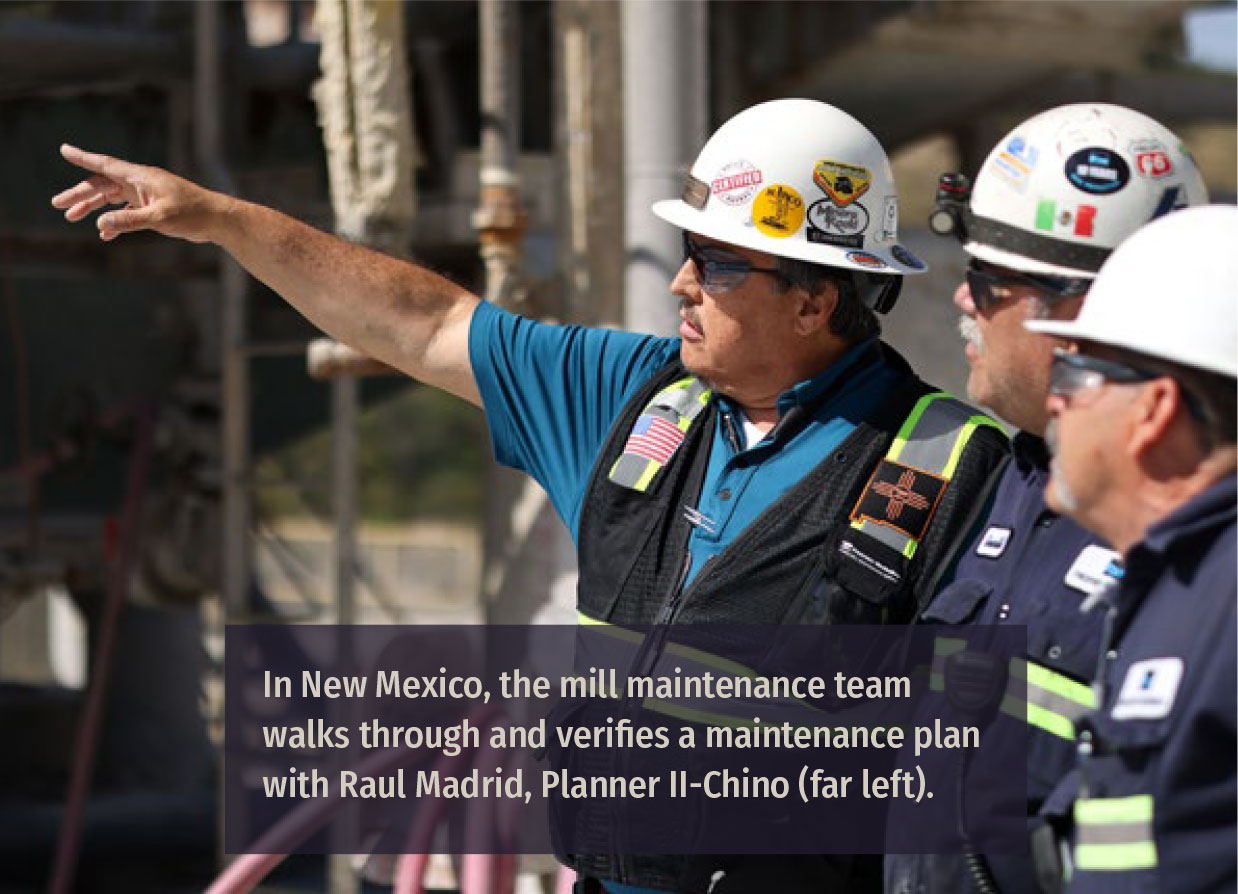
Given that success, it is no surprise that asset efficiency remains key to the Maintenance and Reliability pillar of this year’s strategic themes.
To maintain that momentum, several key initiatives have been identified for the year ahead. Among them, Montes said the company is evolving their process to make managing asset health more simple and transparent, developing governance routines for
increased accountability and updating their site support models to be more hands-on.
“The future of Freeport is being built right now. And it isn’t being built with steel and concrete, but with discipline, by being proactive and demonstrating a relentless commitment to making the most of what’s already in place.”
JUN MONTES | GENERAL MANAGER MAINTENANCE-FM AMERICAS
Inside the company, the team is making their root cause analysis process more effective by going beyond the physical aspect of equipment failure and focusing on process and management gaps.
Strategies also are being implemented at the site level, such as efforts to digitize, standardize and refine maintenance plans instead of relying on individualized knowledge.
Ultimately, the goal is to demystify the maintenance and reliability process at every level.
While the company already has seen the benefit of a move toward such a strategy, Montes sees that progress as just the beginning.
“The future of Freeport is being built right now,” Montes said. “And it isn’t being built with steel and concrete, but with discipline, by being proactive and demonstrating a relentless commitment to making the most of what’s already in place.”
Employee Experience
Management Roadshow Helping Map Future
The landscape of mining is shifting – and not just because of the earth the company moves, but because of the how and the who behind it. Once, success in mining was determined by expediency, and fortune favored those who staked their claims early. Now, that success is determined over decades, and long-term sustainability is the result of careful resource management.
With the future in focus, much attention has turned to workforce development, and efforts now are underway to revive an initiative that could help the company tap into the resources already being developed. Through recurring site visits, the goal of that initiative was to expose more employees to a pipeline of leadership.
Part of that meant networking, with site and corporate leadership meeting with high-potential employees to discuss their personal and professional goals. It also was about providing guidance as well.
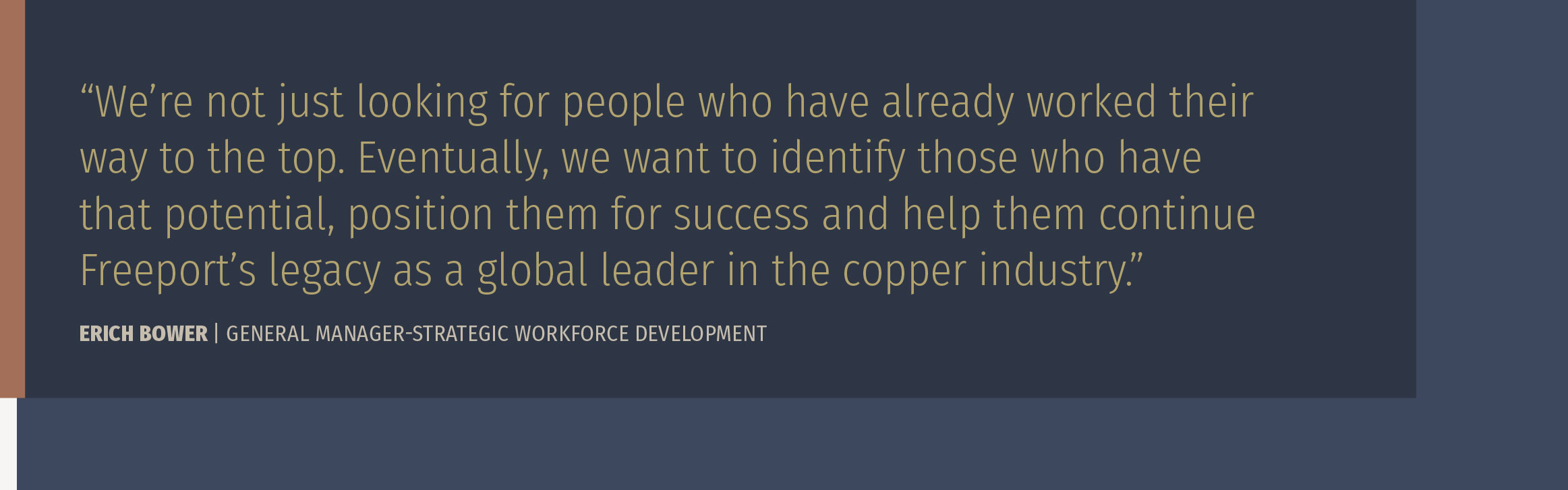
For Swen Gunderson, Director-HR Business Partner, restarting the conversations with senior leaders at our sites will help ensure everyone is aligned with interests, abilities and future progression opportunities.
“Having a venue for our leaders to discuss their career paths and development opportunities is critical as we fill roles,” Gunderson said. “Every person is ultimately responsible for their career, but we want to make sure moves match the desires and personal lives of those making the change. This program fosters those crucial interactions and networking opportunities.”
After a pause during the COVID pandemic, this new “GM Roadshow” is starting small. While this is the first time that senior supervisors have been included, the visits remain limited, with only a select group of senior leaders invited to each event. Visits should rotate through each site at least every two years.
However, that may not always be the case.
According to Erich Bower, General Manager–Strategic Workforce Development, the plan is to grow the program over time. Once a better cadence is established, its scope could expand, providing site leadership with additional opportunities to identify more rising stars.
“We’re not just looking for people who have already worked their way to the top,” Bower said. “Eventually, we want to identify those who have that potential, position them for success and help them continue Freeport’s legacy as a global leader in the copper industry.”
On that front, the company already is seeing promising signs.
While Bower notes that previous iterations of the roadshow have had countless success stories over the years, the biggest for him is what they are hearing from employees right now.
“When we ask folks what would make them consider leaving, so often the answer is nothing,” Bower said. “People feel like they’re being supported, like they’re being given opportunities, and they appreciate the fact that we’re there talking to them. Creating a culture where our employees know just how much they’re valued really is the best metric.”
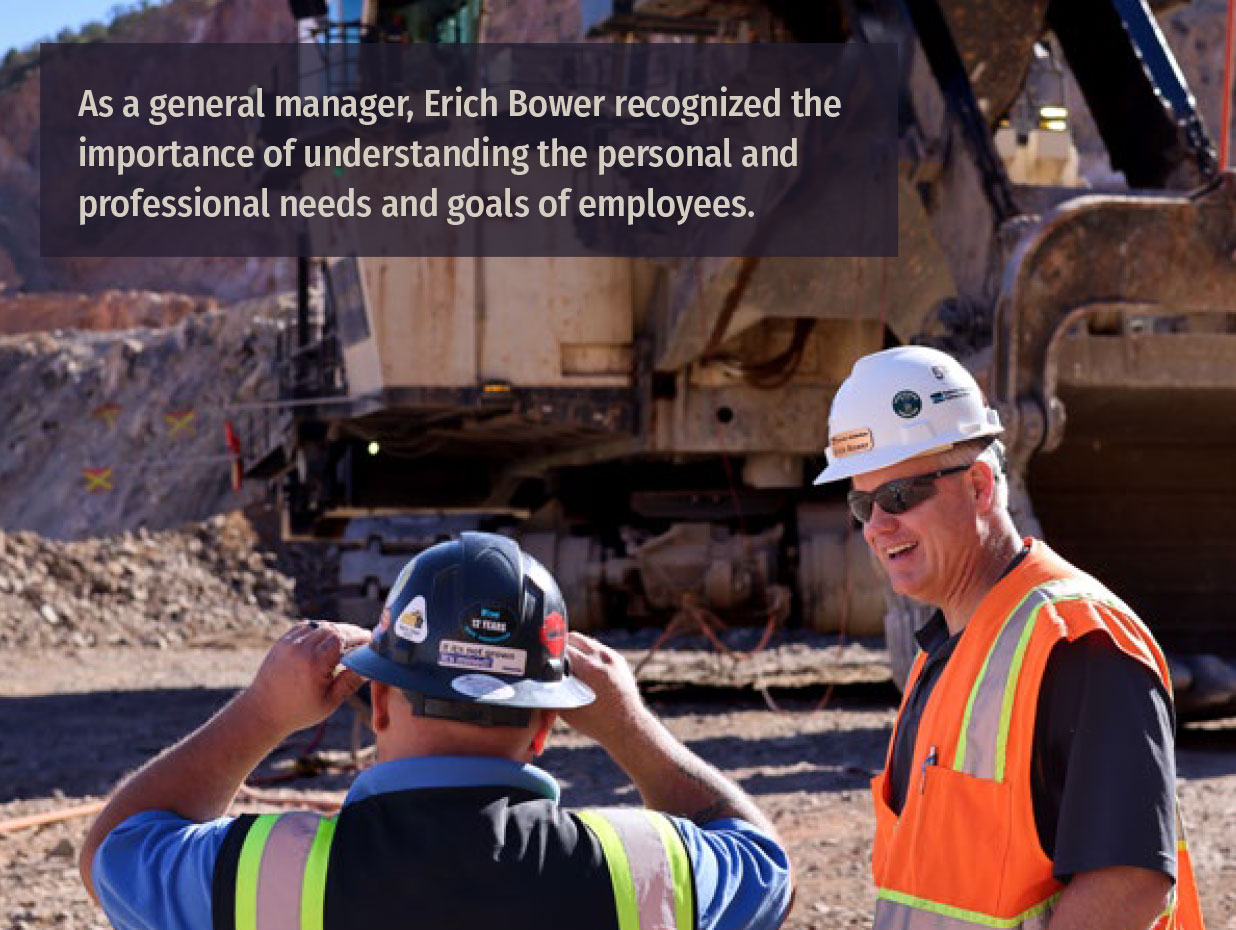
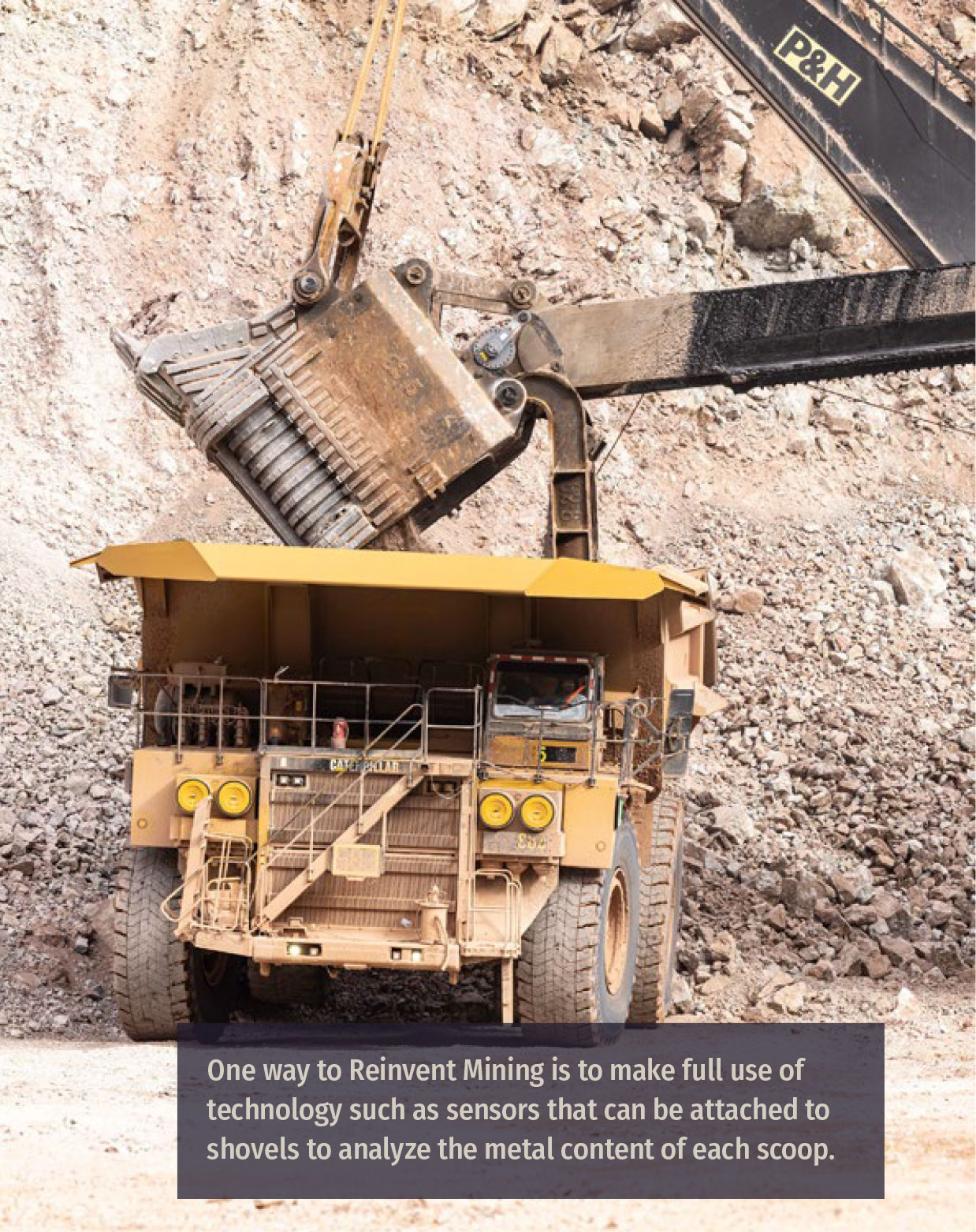
Reinvent Mining
Maximizing Technology and Innovation to Manage Costs
Integrating innovation and the new technologies of the future while being Best at the Basics of production today is Freeport’s way to Reinvent Mining, a comprehensive approach to mining that re-evaluates the old way of doing things to improve production, cut costs and ensure long-term competitiveness.
Reinvent Mining is more than just modernizing equipment or embracing recent technology, said Bert Odinet, Senior Vice President and Chief Innovation Officer. It is a new and dynamic way of thinking about how copper is produced from the shovel to the finished product to determine what is needed to make the entire process more efficient.
Rather than looking at a mining operation as individual functions – blasting, digging, hauling, milling, metal extraction, transporting – it analyzes the entire process from start to finish and identifies the best approaches to maximize value. That might be by using more efficient or cost-effective ways to move ore from the shovel to its destination. It might be developing new ways to extract the copper, as is being done through Freeport’s Leach to the Last Drop work. Or it might be through the better use of technology or data.
“Reinvention is appropriate because it takes a bunch of innovations that have evolved over time in both process and technology, which weren’t available to us when we originally designed our operations, and thoughtfully applies them to our current state to enable greater efficiency,” Odinet said. “Right along with our critical Best at the Basics work, we are going to be applying technology to drive efficiencies and rethink how the organization leverages the ore bodies and the assets that we have to mine more effectively into the future.”
Reinvent Mining to lower production costs is so critical to the company’s future that it has been added as a fifth pillar to Best at the Basics, strategic themes to help safely achieve production goals in the Americas. With mines in North America facing inflationary costs, longer haul runs and declining ore grades, it is imperative to develop ways to produce more copper at less cost.
The goal of Reinvent Mining is to achieve a production cost reduction of 10 cents per pound in Morenci – where the ideas will be tested – by the end of the first quarter this year. An additional 15 cents per pound of cost savings is anticipated by the end of 2025. The current aspiration is to add another 50 cents per pound of opportunities by the end of 2026 through the reinvented mining processes. Long term, the goal is to use process integration, innovations like Leach to the Last Drop and new technology to cut copper production costs in half.
“Reinvention is appropriate because it takes a bunch of innovations that have evolved over time in both process and technology, which weren’t available to us when we originally designed our operations, and thoughtfully applies them to our current state to enable greater efficiency.”
Bert Odinet | Senior Vice President and Chief Innovation Officer
For instance, there are sensors that can be attached to shovels or conveyors that analyze each scoop of ore for its copper content and other minerals. However, if there is no way to sort the ore, that information is largely useless. The sensors become a nuisance and maintenance liability.
But, if the ore distribution system could be reconfigured in a way that allows more precise front-end sorting of ore grades so they can be processed in the most cost-efficient manner, the sensors become the vital first step in the chain.
For the short term, technology maturation teams are assessing what technologies are available now and which emerging technologies are worth investing in and preparing for, Odinet said. They also are planning ways to use that technology at scale in a large mine like Morenci.
“If we are going to be competing into the next century, we need to be really focused on how we apply these innovations and these technologies, especially in understanding what’s happening in our ore bodies,” he said. “Because as grades decline and as hauls increase, we are going to be challenged with cost issues if we aren’t doing things better and smarter.”
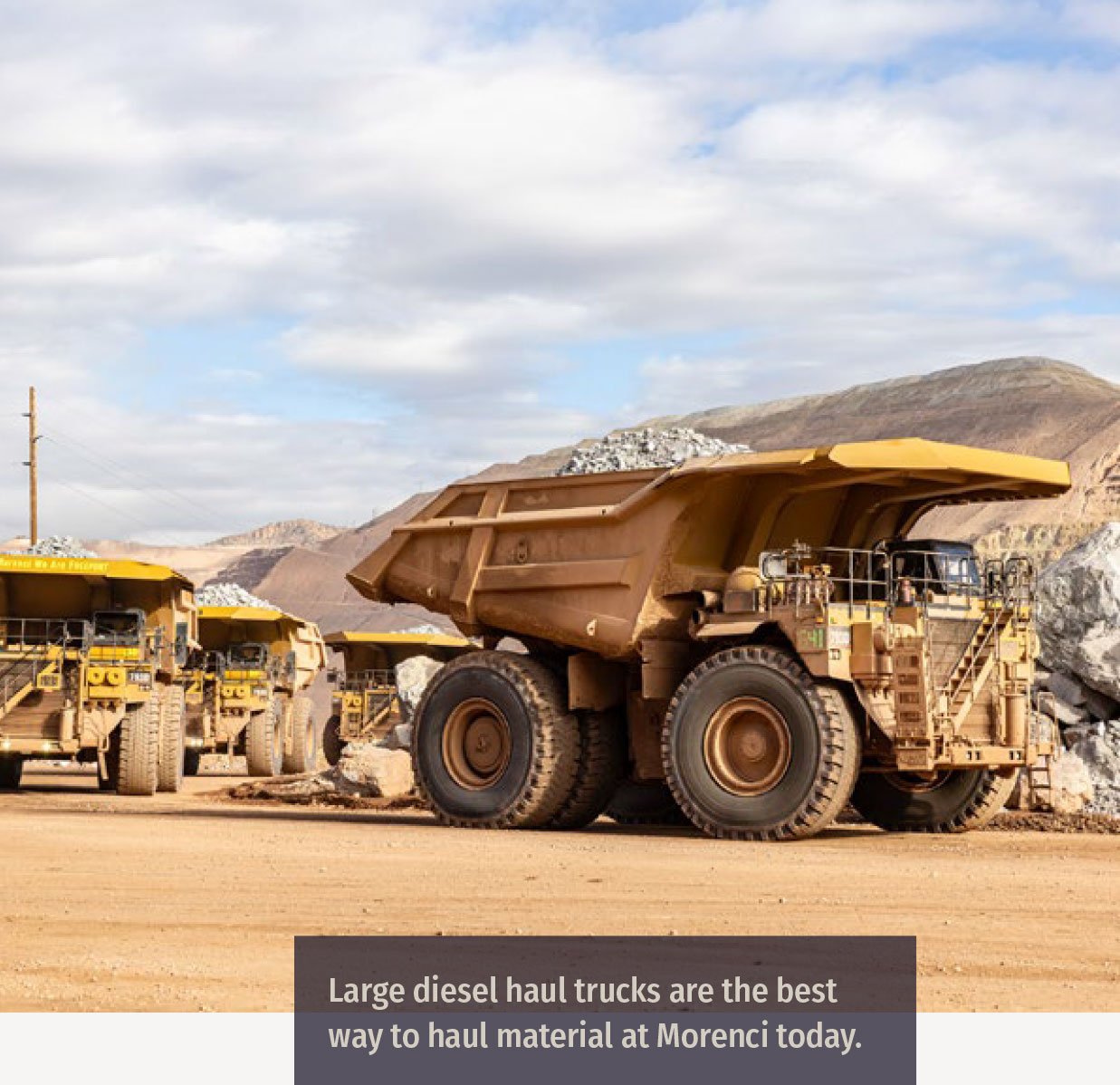
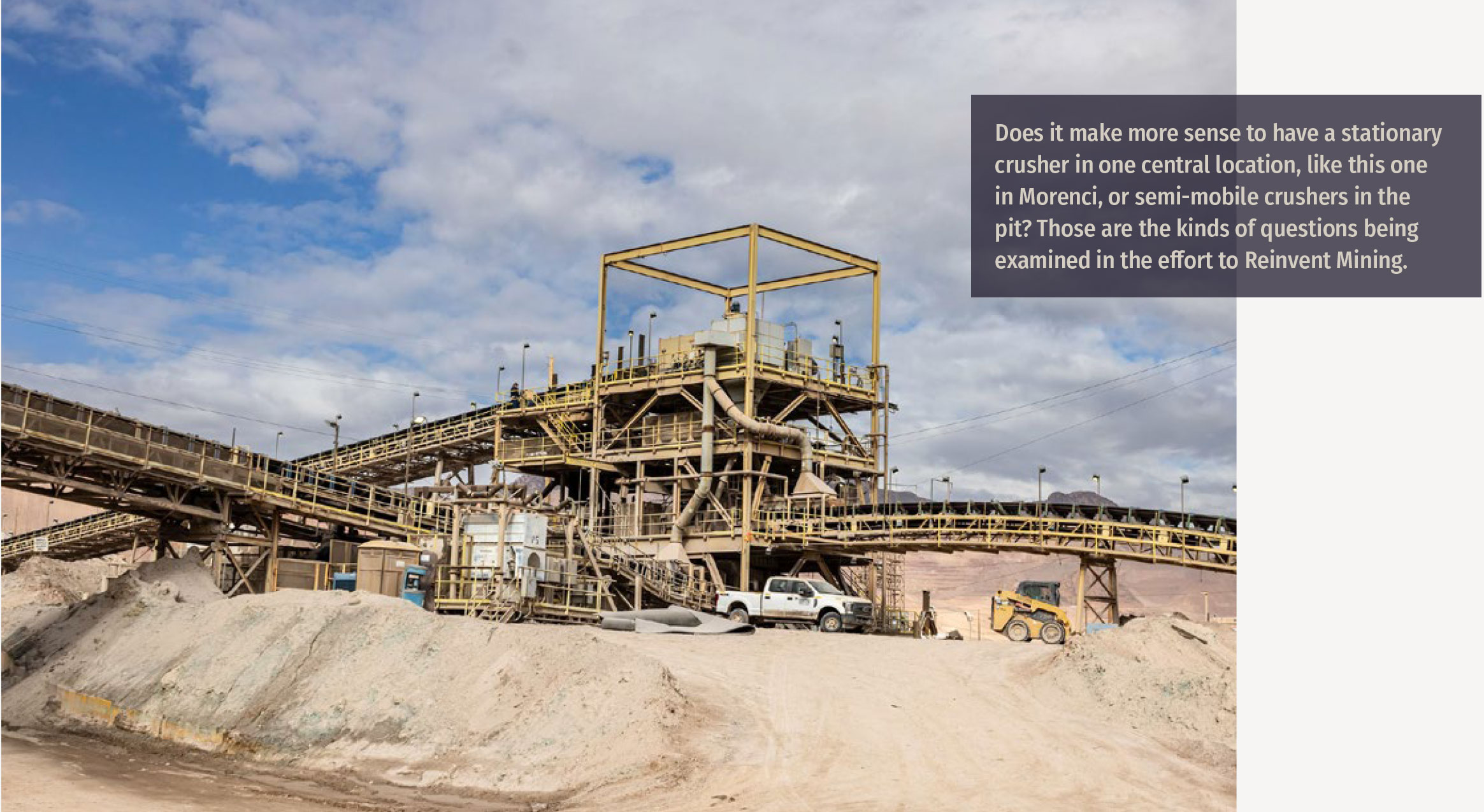